Hydrogen Pipes, Tanks & Vessels
K-TIG provides a narrow root bead and minimal heat-affected zone (HAZ) substantially reducing the susceptibility to hydrogen atom infusion into the weld
K-TIG welding is a specialized welding process that can be used to mitigate the effects of hydrogen embrittlement in certain applications. Hydrogen embrittlement is a phenomenon where hydrogen atoms penetrate the crystal lattice of a metal, causing it to become brittle and prone to fracture, which can be a significant concern in high-strength steel and other materials used in various industries.
In the evolving landscape of carbon steel welding, the introduction of the ASME B31.12 2019 standards marked a watershed moment. Among the myriad criteria introduced, the Vickers hardness maximum limit of 200HV has emerged as a linchpin for safety and longevity in hydrogen transport systems. However, these stringent standards posed a formidable challenge for existing welding technologies.
K-TIG achieved a Vickers hardness performance of 196HV in 6-inch A333 grade 6 carbon steel with a 7.11mm thickness in mechanical testing performed by Bureau Veritas.
The advantages of our welding technology specific to Hydrogen applications include:
- Low Heat Input: K-TIG welding employs a highly concentrated, high-energy-density arc that provides deep penetration into the base material while maintaining a low overall heat input. The reduced heat input minimizes the time that the material is exposed to high temperatures, which is critical in preventing the diffusion of hydrogen into the weld zone. Lower heat input also reduces the risk of cracking associated with hydrogen embrittlement.
- Reduced Hydrogen Absorption: The narrow, deep weld bead produced by K-TIG welding limits the volume of material exposed to the surrounding environment. With less material exposed, there are fewer opportunities for hydrogen to diffuse into the metal structure. This helps in reducing hydrogen absorption, which is a key factor in hydrogen embrittlement.
- Precise Control: K-TIG welding allows for precise control over welding parameters, such as amperage, wire feed rate, and travel speed. This control can be optimized to create a weld with minimal heat-affected zones and reduced residual stresses, further minimizing the risk of hydrogen embrittlement.
- Clean Environment: K-TIG welding is typically performed in an inert gas atmosphere, which creates a clean and protective environment around the weld zone. This inert gas shielding prevents the ingress of atmospheric gases, including hydrogen, during the welding process.
- High-Quality Welds: K-TIG welding is known for producing high-quality, full-penetration welds with minimal defects. Properly executed K-TIG welds are less likely to contain imperfections that could serve as initiation points for hydrogen-induced cracking or embrittlement.
- Reduced Post-Weld Heat Treatment: Traditional welding processes often require post-weld heat treatment to relieve residual stresses and temper the metal, which can be a source of hydrogen embrittlement. With K-TIG welding's lower heat input and reduced distortion, the need for extensive post-weld heat treatment may be diminished or eliminated.
- Material Compatibility: K-TIG welding can be used with a variety of materials commonly used in hydrogen tanks, pipes, and vessels, such as high-strength steels and stainless steels, provided the appropriate process parameters are selected.
For improved operating efficiencies of your pipes, tanks & vessels, use the form below to tell us about your application.
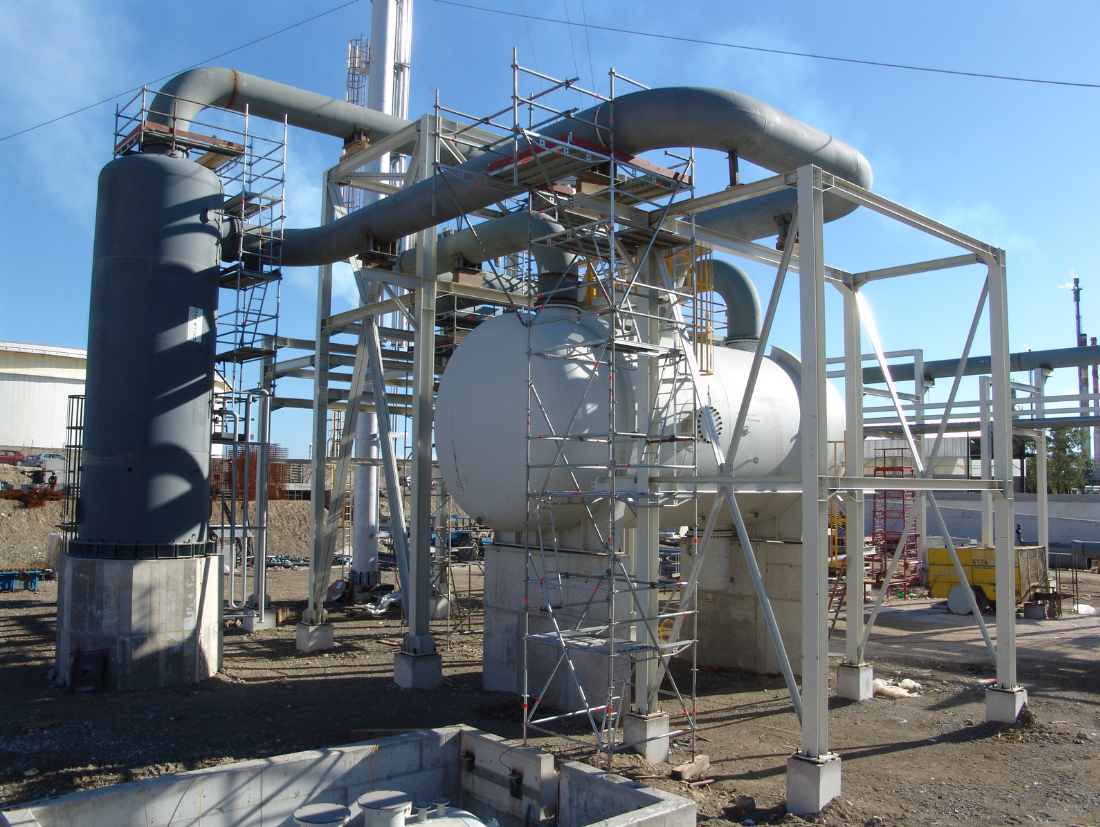
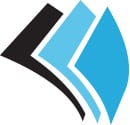